Vol 9 No 2 2024-5
2024.09.02.5
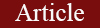
Análisis de riesgos operacionales en una planta procesadora de sábila.
Operational risk analysis in an aloe vera processing plant.
Noel Acacio-Chirino1/* ; Jonnattan Cancino-Camperos 2 .
1Universidad Nacional Experimental Francisco de Miranda UNEFM
2Grupo de investigación ingeniería de riesgo, Universidad Nacional Experimental Francisco de Miranda UNEFM, Venezuela;
*Correspondencia: noelacacio@correo.unefm.edu.ve.
Avaliable form. http://dx.doi.org/10.21931/RB/2024.09.02.5
Resumen
La investigación tuvo como objetivo diseñar un análisis de riesgos operacionales (Hazop) de los procesos de una planta de productos a base de sábila con el propósito de identificar aquellos peligros potenciales y significativos en las operaciones implicadas en el procesamiento de sábila. Se diagnosticó la situación actual de las operaciones de la planta, se identificaron los nodos del proceso, se analizaron las consecuencias de las desviaciones encontradas en los nodos identificados y se formularon las medidas preventivas y recomendaciones para disminuir la tolerancia a niveles aceptables. Un equipo multidisciplinario revisó la información contenida en los diagramas disponibles, entregados para su estudio utilizando la metodología hazop. La información se registró en matrices de riesgo, tomando en cuenta los criterios de severidad y de frecuencia de ocurrencia para establecer los niveles de riesgo. A partir del diagnóstico de los procesos se encontraron situaciones de riesgo con condiciones de operación críticas como altas temperaturas, altas presiones, que pueden provocar accidentes. Se definieron diez (10) nodo equipos, a partir de cuyo análisis se documentaron cuarenta y un (41) recomendaciones, cuatro (04) correspondientes a riesgo reducible y treinta y siete (37) de riesgo bajo. No se identificaron recomendaciones de riesgo intolerable ni de riesgo alto.
Palabras clave. Análisis; hazop; peligros; procesos; riesgos; sábila.
Abstract
The objective of this research was to design an operational risk analysis (Hazop) of the processes of an aloe-based product plant with the purpose of identifying potential and significant dangers in the operations involved in aloe processing. The current situation of the plant operations was diagnosed, the process nodes were identified, the consequences of the deviations found in the identified nodes were analyzed, and preventive measures and recommendations were formulated to reduce tolerance to acceptable levels. A multidisciplinary team reviewed the information contained in the available diagrams, which were prepared for study using the hazop methodology. The information was recorded in risk matrices, considering the criteria of severity and frequency of occurrence to establish risk levels. From the diagnosis of the processes, risk situations were identified under critical operating conditions, such as high temperatures and high pressures, which can cause accidents. Ten (10) node teams were defined, from whose analysis forty-one (41) recommendations were documented, four (04) corresponding to the reducible risk, and thirty-seven (37) of low risk. No intolerable risk or high-risk recommendations were identified.
Keywords. Analysis; hazop; dangers; processes; risks; Aloe Vera.
Introducción
Los hechos que ponen en riesgo la vida o la salud del hombre han existido desde siempre. En consecuencia, también desde siempre, el hombre ha tenido la necesidad de protegerse. Pero cuando estos hechos o condiciones de riesgo se circunscriben al trabajo, históricamente, el tema de la producción ha recibido mayor importancia que el de la seguridad, ya que es sólo recientemente que el hombre, como persona natural y como persona jurídica, ha tomado conciencia de la importancia que reviste la salud ocupacional y la seguridad en el trabajo1.
En épocas más recientes y con el inicio de la era industrial, los cambios en las condiciones de trabajo fueron mucho más drásticos que los acontecidos hasta entonces, los trabajos en las fábricas e industrias aumentaron considerablemente los riesgos, evidenciando la necesidad de tratamientos específicos a estas nuevas situaciones.
Los accidentes y las enfermedades profesionales se convirtieron en aspectos importantes del nuevo mundo laboral, y es ese proceso de industrialización, lo que trajo consigo el uso de equipos y sustancias que constituyeron factores de riesgo para las personas que las manipulan y al ambiente.
Las consecuencias de estos accidentes suelen ser: pérdidas de vidas o daños a la salud humana, impactos ambientales negativos, perjuicios económicos, efectos psicológicos en la población, comprometimiento de la imagen de la industria y del gobierno2.
En Venezuela, esta situación se puede evidenciar al observar el auge industrial no sólo de las grandes industrias, sino de la pequeña y mediana empresa, en las cuales también se realizan actividades que de una u otra forma representan situaciones de riesgo para los trabajadores que muchas veces desconocen las medidas de seguridad en el trabajo que realizan, lo cual se traduce en accidentes y a largo plazo, en enfermedades derivadas de las actividades que realizan.
El análisis de riesgos se emplea para identificar los peligros y amenazas del proyecto y/o instalación, considerando las sustancias peligrosas, condiciones operativas y los posibles peligros, así como las salvaguardas, medidas de seguridad y protecciones consideradas para cada una de las áreas que conforman la instalación, Hazop es una técnica cualitativa para identificar riesgos, permite un análisis más sistemático de las desviaciones de proceso que pueden producirse, sus causas y defensas contra las mismas. Si estas son significativas y las salvaguardas son inadecuadas o insuficientes, se deben recomendar acciones para reducir el riesgo. Los resultados deben ser una lista que contenga los hallazgos representativos donde se identifican los riesgos del proceso, las desviaciones operativas, las causas, las consecuencias, las salvaguardas y las recomendaciones3.
Los objetivos del hazop son los siguientes4:
1.- Detectar riesgos, sus orígenes, sus consecuencias y sus remedios mediante análisis, cualitativo pero sistemático y escrupuloso (si se hace bien), que considera el meollo del proceso que son las desviaciones de sus variables.
2.- Facilitar, al discernimiento de los analistas, decidir cuáles de ésos deben ser objeto de análisis más afinado mediante métodos más detallados y/o cuantitativos.
En un sitio de trabajo donde se cuente con más de diez trabajadores, los Empleadores están obligados a realizar las gestiones pertinentes para la prevención de riesgos ocupacionales, operacionales, ambientales y de procesos, además de velar por la salud, seguridad e higiene del personal laboral; hecho que se ampara en el código de trabajo5.
La técnica del hazop es el método disponible de análisis de riesgos más riguroso, pero no puede proporcionar la seguridad completa de que todos los riesgos han sido identificados ya que el resultado del estudio depende fundamentalmente del desempeño del equipo. El hazop es un trabajo de equipo y el éxito o fracaso del mismo es de todo el equipo6.
Los cambios a la metodología hazop plantean un gran inconveniente; y es que pone en duda la rigurosidad del estudio en sí; queda a criterio del moderador y su análisis previo el cómo dividir los nodos y cuales desviaciones son las más importantes para llevar al equipo multidisciplinario, pudiendo pasar por alto de manera involuntaria desviaciones que potencialmente podrían ser importantes o incluso críticas7.
Con el fin de conocer la aplicación de la metodología de Hazop en la industria, un análisis de los riesgos asociados en los procesos de producción de acetileno se desarrolló en la empresa AGA S.A.8, donde deben contar con sistemas de seguridad, salud e higiene ocupacional que permitan la óptima protección de la salud de los trabajadores, contra riesgos de naturaleza física, química, mecánica, eléctrica, ergonómica y ambiental, debido a que en las plantas de acetileno de baja y alta densidad son instalaciones que por su naturaleza de sus procesos incluyen muchos puntos vulnerables a la presencia de riesgos de fuga, incendio, explosión y dispersión tóxica, siendo los eventos que agravan estos riesgos en la planta las variaciones de operación de los equipos y procedimientos que pueden originar una alteración en el funcionamiento del proceso.
La empresa AGA S.A. requiere de un sistema que garantice el cumplimiento de las desviaciones encontradas fuera del estándar internacionales como de los aplicados internamente para incrementar la protección de los trabajadores y optimizar los procesos en el área de manufactura de acetileno, para lo cual se describen los principales indicadores de gestión del Sistema de Seguridad y Salud Ocupacional de la compañía, a través del análisis de los riesgos de la planta de acetileno, utilizando como técnicas, el panorama de riesgos, el método de William Fine, el método Hazop, la Norma ISO 9001: 2008, reporte de accidentes e incidentes de la planta y el check list para auditar riesgo de incendio en la planta de acetileno y el Método simplificado de evaluación de riesgo de incendio Meseri.
Después de haber analizado los principales riesgos de la planta de acetileno, se identifican las causas y consecuencias del problema referido al sistema de salud y seguridad ocupacional de la empresa, utilizando las técnicas de diagnóstico mencionadas anteriormente, más los diagramas de Ishikawa y Pareto.
Una vez que se ha llevado a cabo el diagnóstico de la situación actual de la planta de acetileno, se elabora la propuesta la cual consiste en considerar el cumplimiento de las distintas auditorías realizadas en la planta de acetileno, para mejorar las condiciones de protección de los trabajadores ante los riesgos de seguridad y salud de toda la empresa y las zonas aledañas.
A partir del diagnóstico los principales factores de riesgo laborales en la planta de acetileno, son riesgo de incendio y de contaminación con gas acetileno por la manipulación inadecuada de los cilindros y equipos que corresponden a los tipos eléctrico, químico y mecánico, los cuales pueden ocasionar conatos, afectar a la salud de los empleados en las vías respiratorias y piel, así como golpes y caídas, lesiones graves e incluso la muerte, si están fuera de control.
La aplicación de la técnica Hazop permitió identificar 32 nodos a partir de lo cual se recomiendan 273 acciones para disminuir los riesgos a niveles aceptables.
La propuesta para la compañía, consiste en el análisis de riesgos en los procesos de producción del acetileno y propuesta de elaboración de un manual de procedimientos, para controlar los riesgos laborales de mayor incidencia, el cual incluirá medidas de seguridad para la formación, capacitación y motivación del talento humano, además del control del uso de los equipos de protección personal y la adquisición de detectores de flama, de fugas de acetileno y manómetros, para mantener controlados los riesgos en la planta y prevenir adecuadamente los accidentes de trabajo y las enfermedades ocupacionales.
Esta investigación permite analizar los riesgos en planta no solamente mediante la técnica hazop, sino que permite la localización y priorización de los riesgos mediante otras técnicas para evaluación de riesgos. También se apoya en herramientas de sistemas de gestión a fin de diagnosticar las causas y efectos de los problemas y la evaluación económica para la aplicación de medidas propuestas de seguridad, salud e higiene del trabajo para el control óptimo de los riesgos en la planta de acetileno, lo cual sirve de referencia para el análisis de riesgos en fábricas de menor complejidad.
En un diagnóstico y evaluación ocupacional de un laboratorio farmacéutico9, donde no se contaba con ningún sistema de análisis de riesgos o de seguridad ocupacional y se realizó una evaluación de la situación actual del laboratorio. Se revisaron los registros históricos de accidentes en el laboratorio. Posteriormente, se realizó una evaluación de la situación actual del laboratorio. Esta tarea gozó de buena aceptación por parte de los directivos, quienes manifestaron su interés por conocer el estado de su empresa en cuanto a instalaciones, equipo de protección personal (EPP), atención a emergencias y salud ocupacional.
Se desarrollaron cuatro cuestionarios, los cuales abarcaron los temas de interés, además de otros propios del área de almacén. Tales cuestionarios coadyuvaron en precisar un diagnóstico de la situación actual de la empresa. Se evaluaron las respuestas. Con ellas se hicieron las debidas correspondencias con los datos históricos de los accidentes. Por último, se realizaron las recomendaciones pertinentes con el fin de evitar accidentes posteriores.
Esta investigación proporciona información relevante, ya que se presenta una situación similar a la presentada en la fábrica para procesamiento de sábila, con lo que la forma de abordaje de la situación del laboratorio puede servir como referencia a la hora de diagnosticar la situación de los procesos de la fábrica. También aporta aspectos teóricos como los métodos de análisis de riesgos (OWAS, Hazop, métodos probabilísticos, método de la EPA, método encuesta-auditoría. También describe la metodología para los análisis de riesgos, así como los lineamientos para la elaboración de un manual de riesgos.
Un estudio de riesgos y operatividad hazop que se realizó para la unidad de regeneración de aminas (ARU) a ser construida en un complejo petroquímico y refinador en la provincia de Manabí, Ecuador10. Para lo cual se revisaron los diagramas de instrumentación y proceso (P&IDs), se procedió a categorizar cada escenario del proceso usando la matriz de riesgos que la empresa posee dentro del Sistema de Riesgos. En esta etapa no se consideran las salvaguardas existentes y futuros escenarios para reducir riesgos. En este análisis se hicieron un total de 14 recomendaciones y 14 parking lot dando un total de 28 puntos de acción para esta unidad. Con este análisis se conocen las causas y las consecuencias de un fallo en un sistema y es más sencillo evitarlo, y poder introducir las salvaguardas adecuadas para prevenir este fallo. Estas salvaguardas deben ser apropiadas al riesgo existente y deben permitir alcanzar a su vez altos niveles de disponibilidad de la planta. Las recomendaciones fueron hechas con la intención de prevenir causas o mitigar consecuencias, proponiendo la implementación de medidas de reducción de riesgos suficientes y adecuadas al proceso
Esta investigación permite tomar en detalle aspectos propios de la técnica hazop y su metodología, así como el uso de la matriz de riesgos y la forma de realizar recomendaciones a partir del análisis realizado.
Estas investigaciones permiten servir como un punto de apoyo a este trabajo de investigación ya que en existen investigaciones sobre análisis hazop en plantas de alimentos a ase de sábila, teniendo en cuenta que son trabajos aplicados a plantas de mayor complejidad, donde los procesos se dan en condiciones extremas y que representan mayor peligrosidad. Por otra parte, se debe tener en cuenta que los análisis de riesgos no limitan su aplicación a pequeñas o grandes plantas o fábricas, como es el caso de la planta para el procesamiento de sábila, aun cuando la magnitud de los riesgos que afectan al proceso no es grave, si son importantes determinarlos, pues de ellos depende la calidad del producto, teniendo en cuenta que es un producto alimenticio11.
Para llevar a cabo el procesamiento de sábila, la planta procesadora cuenta con una serie de equipamientos que van desde el área de procesamiento de la materia prima, procesamiento primario, líneas de proceso principales (gel de sábila, trocitos de gel, jugos), secado de restos de corteza, pasando por el área de mezcla y envasado, área de fabricación de envases e instalaciones de servicios auxiliares. Muchos de estos procesos involucran operaciones de escaldado, tratamientos con vapor, esterilización, tratamientos UHT, que involucran equipos que conllevan a situaciones de riesgo ya que existen condiciones de operación críticas como altas temperaturas, altas presiones, riesgos eléctricos, manejo de combustibles, donde la planta no tiene documentada, revisada ni actualizada la identificación de riesgos y problemas operativos en los procesos que realizan.
Por otra parte, para poder cumplir con las certificaciones y permisos reglamentarios establecidos en las normativas venezolanas, se requiere una información detallada de los aspectos relativos a la ingeniería de riesgo, a fin de dar cumplimiento y resguardar la integridad de todo el personal que labora en la fábrica.
El propósito de este trabajo es desarrollar un análisis de riesgos operacionales Hazop, (de HAZard and OPerability analysis) de los procesos de una planta procesadora de sábila, a fin de analizar sistemáticamente las causas y las consecuencias de las desviaciones de las variables de los procesos de la fábrica y controlar los riesgos operacionales que puedan afectar a las personas, a la comunidad, a los bienes físicos y al medio ambiente.
Materiales y métodos
Se conformó un equipo multidisciplinario de análisis integrado por 7 ingenieros, con experiencia en la operación del sistema y de los equipos, experiencia en la inspección y manutención de equipos, conocimiento de la química del proceso, conocimiento de los objetivos de la seguridad (SIAHO), y experiencia y conocimiento en la técnica hazop (ingeniero de riesgo CRP-PDVSA), y recopilada la información que se utilizó durante el análisis (diagramas de flujo del proceso DFP, procedimientos operativos, procedimientos de emergencia, planos de planta), se procedió a la aplicación de la técnica Hazop.
Se realizaron entrevistas no estructuradas al personal que labora en la planta para conocer detalladamente los procesos realizados y las condiciones bajo las cuales son realizados.
Mediante sesiones de grupo, se aplicaron los principios de la técnica hazop y la información recabada se registró en matrices de riesgo y hojas de registros de resultados hazop y tablas diseñadas según las normas del manual de seguridad industrial12.
La metodología empleada para realizar el análisis hazop en la planta procesadora de sábila se resume en la figura 1.
Figura 1. Metodología para el análisis de Hazop en la planta procesadora de sábila
Fuete: Elaboración propia.
El equipo fija las deviaciones que se consideran necesarias para a aplicación del estudio de Hazop, utilizando las palabras clave que aplican en los procesos, tal como se muestra en la tabla 1.
Tabla 1. Desviaciones consideradas.
Ítem Desviación
1 Alto flujo
2 Bajo/No Flujo
3 Flujo reverso
4 Alta Temperatura
5 Baja Temperatura
6 Alta Presión
7 Baja Presión
8 Alto Nivel
9 Bajo Nivel
Posteriormente al diagnóstico de los procesos e identificación de los nodos, se presentan los criterios de severidad, criterios de frecuencia de ocurrencia, que permiten establecer los niveles de riesgo en cada nodo definido. Esta información se obtiene de las normas de la industria petrolera venezolana 12.
Tabla 2. Criterios de Severidad12.
Posible severidad potencial
Comunidad
Personas Pérdidas oportunidad y Activos Costo total en USD Ambiente Imagen
C P PO A I
1 Olores o ruidos molestos.
Primeros Auxilios o
asistencia médica Breve interrupción a la operación. Perdidas de oportunidad y daños.
<$500 M Afectación Leve
sin amenaza
ambiental –Demanda de un
tercero por <
$ 10M – $100M
–Cobertura mediática
local,
quejas telefónicas de la
comunidad
2 Lesiones menores o
Efectos reversibles a la
salud
Lesión con
tratamiento médico,
sin tiempo
perdido.(TR) Parada de planta menor a 1 semana. Pérdidas de
oportunidad y daños
$500 M < $ 1 MM Contaminación
dentro del límite de batería que puede causar daño
ambiental – Demanda de un
tercero por $ 100 M – $500 M
– Campaña mediática adversa extensiva e ámbito regional
3 Múltiples
lesiones o daños
moderados a la
salud
Múltiples lesiones
serias o
discapacidad
temporal (TP) Parada de planta entre
1 y 2 semanas. Pérdidas de
oportunidad y daños $1 MM < $ 5MM Contaminación
inmediata fuera del
límite de batería – Demanda de un
tercero por
$ 500 M – $5 MM
– Campaña mediática adversa
extensiva e ámbito nacional
4 Al menos una
fatalidad o
discapacidad total
permanente
Al menos una
fatalidad o
discapacidad total
permanente Parada de planta entre 2 y 4 semanas. Pérdidas de
oportunidad y daños $
5 MM <$ 50MM Fuga masiva de
contaminantes,
Daño ambiental
significativo a largo
plazo – Demanda múltiples de terceros que totalizan $5 MM –$50 MM
– Campaña mediática adversa
extensiva en ámbito nacional e internacional.
– Investigación
gubernamental
5 Múltiples Fatalidades o
Daños irreversibles a la salud.
Múltiples fatalidades Parada de planta mayor a 4 semanas. Pérdidas de oportunidad y daños > $50 MM Daño ambiental a gran escala, irreversible –Gerente o Supervisor
privado de libertad
– Demanda múltiples de terceros que totalizan > $ 5 MM
Tabla 3. Criterios de Frecuencia de Ocurrencia12.
Categoría Frecuencia anual Capas de Protección y su Relación con la Frecuencia.
Valor Descripción
A Improbable -Baja probabilidad de que el escenario de riesgos ocurra.
-1 cada 100 años Se cuenta con cuatro o más capas de protección independiente y altamente confiable. La falla de tres capas no debería ser el iniciador de un evento no deseado
B Remoto Puede ocurrir una vez en los próximos 30 años. Se cuenta con tres capas de protección independiente y altamente confiable. La falla de dos capas no debería ser el iniciador de un evento no deseado.
C Probable – Probablemente puede ocurrir (más de una vez en los próximos 10 años). -Se cuenta con una historia de ocurrencia en la industria y con consecuencias asociadas.
Se cuenta con dos capas de protección independiente y altamente confiable. La falla de una capa no debería ser el iniciador de un evento no deseado.
D Ocasional – Alta probabilidad (más de una vez en el próximo año).
– Ha ocurrido durante los últimos 2 años. Para prevenir eventos no deseados se cuenta con una sola capa de protección independiente y la acción del operador.
E Cierto – Muy alta probabilidad (más de una vez por mes).
– Ha ocurrido al menos tres veces durante los últimos 12 meses. Para prevenir eventos no deseados solo se tiene procedimientos operacionales y la acción del operador.
Una vez establecido los niveles de riesgo, para el establecimiento de las medidas preventivas, se tienen los criterios descritos en la tabla 4.
Tabla 4. Criterios para respuesta al riesgo12.
Categoría Nivel riesgo Resolución Descripción
5 Intolerable
Requiere inmediata acción Medidas para reducir el riesgo a un nivel tolerable son mandatorias y se requiere realizar a ACR.
4 Alto
Requiere acción Reducir el riesgo a un nivel tolerable. Las recomendaciones se deben cumplir en un lapso tiempo determinado no mayor a un año, no obstante, se requieren tomar medidas temporales para controlar el riesgo. Se requiere realizar un análisis de consecuencias para definir tipo de estudio.
3 Reducible
(Zona ALARP)
Requiere acción Las recomendaciones individuales o combinación de ellas deben evaluarse mediante la aplicación de un Análisis Costo – Beneficio-Riesgo. Se deben cumplir en un lapso tiempo determinado no mayor a dos años, no obstante, se requieren tomar medidas temporales para controlar el riesgo.
2 Bajo
Acción a discreción del equipo Las recomendaciones individuales o combinación de ellas deben evaluarse mediante la aplicación de un Análisis Costo – Beneficio.
1 Insignificante
No acción
–
Diseño del análisis de riesgos operacionales (Hazop) de los procesos de la planta procesadora de sábila.
Premisas del estudio
Las condicionantes con las que se estuvo de acuerdo y realizó esta identificación de peligros son las siguientes:
• Incendio.
• Daños a personal
• Daños a equipos.
• Pérdida de producción.
• Parada de plantas.
• Paro de proceso.
• Explosión.
• Los sistemas funcionan bien, cuando operan de acuerdo con la intención del diseño.
• Los sistemas funcionan bien, cuando son bien mantenidos en acuerdo a la frecuencia establecida por el mantenedor.
• Los riesgos y problemas de operatividad se generan de las desviaciones a la intención de diseño.
• Se asume que el sistema será operado dentro de los límites de seguridad y de no alarma.
• Se cuenta con operadores capacitados.
• Los procedimientos escritos son adecuados.
• Se cumplen las políticas y normas de la empresa.
Información de seguridad de los procesos
La información de seguridad de los procesos consta de tres aspectos: (1) la química, (2) la tecnología y el (3) equipo del proceso. Para cada uno de estos aspectos existen requerimientos específicos de información que fueron cumplidos para que el análisis sea válido. A continuación, se describen los requerimientos específicos de información revisados para cada uno de estos aspectos.
La aplicación de la metodología Hazop se realizó con apoyo de los diagramas de tuberías e instrumentación, diagramas de flujo de proceso, experiencia de los participantes y los procedimientos operacionales de la unidad.
Documentación del Hazop
Es importante documentar el análisis para apoyar las buenas decisiones de riesgo, para preservar los resultados del análisis para su uso futuro (en revalidaciones) como evidencia de que el estudio se realizó de acuerdo a buenas prácticas y para apoyar otras actividades relacionadas con la administración de riesgos (como la elaboración de procedimientos operativos, la administración del cambio, la investigación de incidentes).
Los resultados del análisis Hazop se presentan normalmente en forma de tablas. Una tabla de formato normal contiene seis columnas: número de ítem, desviaciones, causas, consecuencias, salvaguardas y recomendaciones. En este caso se añadieron las columnas correspondientes a la matriz de riesgo empleada para así presentar la información de forma completa13.
Resultados
La planta procesadora de sábila comprende las unidades productivas tal como se muestran en la figura 2.
Figura 2. Unidades productivas de la planta procesadora de sábila.
Los principales procesos involucran el equipamiento como se muestra en la figura 3.
Figura 3. Principales procesos de producción de gel de sábila con el equipamiento industrial.
Figura 4. Diagrama de flujo de la procesadora de sábila.
La figura 4 muestra la secuencia de etapas en el procesamiento de sábila para las principales líneas de producción, se indican las operaciones requeridas para transformar las pencas de sábila en los productos terminados. Se resaltan los 10 equipos de proceso que a su vez constituyen los nodos de proceso y que permiten la aplicación de la técnica de hazop, analizando las desviaciones en cada nodo definido.
Equipos críticos identificados en la planta procesadora de sábila
A partir del diagnóstico y las condiciones de operación analizadas, mediante una sesión de grupo, se fija la temperatura como variable crítica debido a que es la que presenta variaciones significativas en todos los procesos y a partir de esto, se identifican los equipos que operan a temperaturas sobre los 50 °C ya que a partir de esta temperatura se producen quemaduras profundas14, donde se establecen los siguientes equipos críticos, tomando como patrón tres parámetros, (si la falla es del equipo: detiene la planta en un 100%, si puede causar más de una fatalidad y si ocasiona daño al medio ambiente). Los equipos que cumplieron con por lo menos uno de los parámetros consideraron de alto impacto o críticos. Siendo estos: caldera pirotubular 1, caldera pirotubular 2, horno secador de cinturón de 5 capas, maquinaria de esterilización de tipo plato, hervidor de esterilización (autoclave), maquinaria esterilización UHT de jugo concentrado, máquina de esterilización de jugo de sábila UHT, máquina de esterilización de trocitos de sábila UHT, máquina sistemática de inyección plástica y el soplador-organizador de botellas, los mismos se muestran en la figura 4.
El porcentaje de equipos críticos del área de producción de la planta es de 3,7%, lo cual representa diez equipos de un total de doscientos setenta y ocho (278) equipos pertenecientes al área de operaciones de procesamiento de sábila. De estos equipos críticos el 100% cumple con el criterio de fatalidad y 50% con el criterio de continuidad operativa.
Tabla 5. Listado de secciones o nodos de estudio.
Nodo Intención general del nodo Temperatura de operación Presión de operación
1.- AC CD 01 Caldera Pirotubular 1 Generar vapor para las áreas de procesamiento. 175 °C 827.371- 999.74 kPa
2.- AC CD 02 Caldera Pirotubular 2 Generar vapor para las áreas de procesamiento. 175 °C 827.371- 999.74 kPa
3.- 010507 Horno secador de cinturón de 5 capas Secado de residuo de concha de penca de sábila 90 °C –
4.-010217 Maquinaria de esterilización de tipo plato Concentrar gel de sábila 90 °C –
5.- 010314 Hervidor de esterilización (autoclave) Esterilizar trocitos de sábila 121 °C 2999.22 kPa
6.-010223 Maquinaria esterilización UHT de jugo concentrado Esterilizar gel de sábila 132 °C –
7.- 020501 Máquina de esterilización de jugo de sábila UHT Esterilizar jugo con gel de sábila 132 °C –
8.- 020502
Máquina de esterilización de trocitos de sábila UHT Esterilizar trocitos de sábila 132 °C –
9.- 020701 Máquina sistemática de inyección plástica Elaborar preformas de PET 285 °C 917002.72 kPa
10.- 020703 Soplador-organizador de botellas Fabricar botellas de PET 120 °C 344.738 kPa
Resultados del Hazop
Los resultados del análisis Hazop consisten en una lista de recomendaciones o en un informe completo que describe todas las desviaciones del proceso examinadas.
Tabla 6. Resultados de hazop nodo: 1.- Caldera Pirotubular 1, Planos: 09176D-B04-03, Equipos involucrados: AC CD 01, Desviación: 1. Alto flujo (combustible a la caldera).
Posibles causas P Posibles consecuencias S NR Protección
Control y
Contención Protecciones
Preventivas Protecciones
Mitigación P S NR Recomendaciones Responsabilidad
1. Fuga / rotura en accesorios,
bridas, válvulas en línea de entrada de combustible del quemador C 1.1. emanaciones de humo y gases tóxicos con fatalidades y personas lesionadas 5
P
5 1.1.1. Drenaje
fuera de la
caldera. 1.1.1. Alarma y disparo de la P04C0106~07por bajo
Flujo. 1.1.1. Sistema
fijo
contra incendio.
1.1.2.
Procedimiento
operacional/
emergencia. B 4
P
3 1. Realizar
procedimientos de
emergencias en sala de calderas Supervisor sala de calderas
C 1.2. Formación de una piscina de fuego con posibilidad de un pool fire.
5
P
5 1.1.2. Drenaje
y pendiente
hacia un lugar
fuera del área de la caldera.
1.1.1. Alarma y disparo de la P04C0106~07por bajo
Flujo. 1.2.1. Sistema
fijo
contra incendio. B 3
P
O
3 2. Revisar y/o
actualizar los planes
de emergencia para
eventos mayores en
el cual se vea
afectada la
comunidad.
3. Incorporar la formación de personal en situaciones de emergencia.
4. Evaluar la
factibilidad de
instalar un sistema
de rociadores que
proteja la AC CD 01 activado a través de un sistema
de detección de
fuego. Supervisor de SHIAO
Tabla 7. Resultados de hazop Nodo 1: Caldera Pirotubular. Nodo: 1.- Caldera Pirotubular 1, Planos: 09176D-B04-03, Equipos involucrados: AC CD 01, Desviación: 4. Alta Temperatura, Intención de Diseño Parámetro: 193 °C.
Posibles causas P Posibles consecuencias S NR Protección
Control y
Contención Protecciones
Preventivas Protecciones
Mitigación P S NR Recomendaciones Responsabilidad
1. Incrustaciones en la tubería C 1.1 Rotura de las tuberías
1.2 Parada de planta
3
P
O 3 1.1.1Parada
De mantenimiento general cada 4 años. 1.1.1.
Capacitación
personal 1.1.1.
Procedimiento
operacional C 1
P
O 2 5. Incorporar
el plan de
mantenimiento
preventivo la
caldera AC CD 01 Supervisor sala de calderas
2. Falla en el sensor de temperatura a la salida de la chimenea C 2.1 Explosión
2.2 Múltiples fatalidades 5
P 5 2.1.1. Plan de
Mantenimiento instrumentación. 2.1.1.
Capacitación
Personal. 2.1.1.
Procedimiento
Operacional.
2.1.2.
Procedimiento
operacional/
emergencia. C 1
P
O 2 6. Incluir en el
planeamiento previo
el escenario de
explosión en la caldera AC CD 01
7. Incluir plan de formación para los
operadores de calderas.
8. Incluir un stock de repuestos asociado al sistema de control de temperatura. Coordinador de SHIAO
Tabla 8. Resultados del hazop Nodo: 3.- Horno secador de cinturón de 5 capas, Planos: 09176D-P01-02, Equipos involucrados: 010507, Desviación: 6. Alta Presión (vapor a las válvulas), Intención de Diseño Parámetro: 1 MPa.
Posibles causas P Posibles consecuencias S NR Protección
Control y
Contención Protecciones
Preventivas Protecciones
Mitigación P S NR Recomendaciones Responsabilidad
1. Fuga / rotura en accesorios,
bridas, válvulas de vapor al horno.
C 1.1. Sobrepresión en la línea, Fuga de
vapor. Posibles daños
mecánicos en la línea por
expansión térmica. 4
P 4 1.1.1.
Capacitación
personal 1.1.1.
Mantenimiento preventivo de las válvulas de vapor.
1.1.1.
Procedimiento
Operacional D 1
P 2 19. Evaluar la
factibilidad de
instalar un sistema de seguridad en las válvulas de vapor del horno.
20. Identificar las válvulas de
vapor y colocar
avisos y precintos
de seguridad en las
mismas
Gerente de Operaciones
Tabla 9. Principales recomendaciones, responsables y nivel de riesgo (NR) asociado.
Recomendación Usada en Responsabilidad NR
1. Realizar procedimientos de
emergencias en sala de calderas Posibles causas:
1.1.1, 2.1.1 Supervisor sala de calderas 3
2. Revisar y/o actualizar los planes
de emergencia para eventos mayores en el cual se vea afectada la comunidad.
Posibles causas:
1.1.1, 2.1.1 Supervisor de SHIAO ( Seguridad Industrial, Ambiente e Higiene Ocupacional) 3
3.Incorporar la formación de personal en situaciones de emergencia. Posibles causas:
1.1.1, 2.1.1 Supervisor de SHIAO 3
8. Incluir un stock de repuestos asociado al sistema de control de temperatura. Posibles causas:
1.4.2, 2.4.2 Gerente de Operaciones 2
9. Evaluar la instalación de un sistema de alarma por alta temperatura a la salida de la chimenea. Posibles causas:
1.4.2, 2.4.2 Gerente de Operaciones 2
19. Evaluar la factibilidad de instalar un sistema de seguridad en las válvulas de vapor del horno. Posibles causas:
3.6.1 Gerente de Operaciones 2
20. Identificar las válvulas de
vapor y colocar avisos y precintos
de seguridad en las mismas. Posibles causas:
3.6.1 Supervisor de SHIAO 2
Discusión
De acuerdo a lo mostrado en la tabla 9, producto del análisis desarrollado en el estudio hazop no existen recomendaciones relacionadas con peligros con riesgo intolerable (No aceptable) así como de riesgo alto. Las recomendaciones relacionadas con riesgo reducible (aceptables implementando acciones de control) corresponden al 10 % de las recomendaciones cuya implementación debe justificarse con base en análisis de tipo técnico y de costo-beneficio.
Por otra parte, un 90 % de las recomendaciones corresponden a riesgo bajo, es decir aceptable o tolerable. En principio, para este tipo de riesgo no se requieren implementar medidas de control de riesgo adicionales, sin embargo, se recomienda su evaluación a fin de establecer la conveniencia de su implementación, a fin de contribuir con la operación segura y confiable de las instalaciones y equipos de proceso.
Cabe resaltar que el total de las recomendaciones generadas pueden proveer protecciones adecuadas para las condiciones analizadas, pero ello no implica que las partes responsables de desarrollar los planes de acción finales en la planta procesadora de sábila limiten su planificación a la ejecución y cierre de las acciones propuestas, toda vez que puede considerarse necesario incluir medidas adicionales a las que surgieron durante la ejecución del Hazop.
Se debe tomar en cuenta al factor humano como responsable de algunas de las desviaciones y al factor capacitación como una cuestión a mejorar, ya que es necesario que muchas desviaciones estén asociadas a la falta de capacitación15.
Es importante que la metodología hazop deba tener un seguimiento, ya que este permite a la organización evaluar el sistema completo y nos ofrece las medidas correctivas que se deban implementar para que el área se encuentre en un excelente estado16.
Conclusiones
Se determinaron procesos que implican tratamientos con vapor, esterilización, tratamientos UHT, que involucran equipos que conllevan a situaciones de riesgo ya que existen condiciones de operación críticas como altas temperaturas, altas presiones, que pueden provocar accidentes.
Se definieron diez (10) secciones o nodo-equipos de estudio, tomado como variable crítica la temperatura, debido a que es la que presenta variaciones significativas en todos los procesos y es la condición que puede ocasionar accidentes.
Se detectaron peligros asociados a diferentes tipos de riesgo: riesgo intolerable (no aceptable), riesgo alto, riesgo reducible y riesgo bajo.
Se formularon 4 recomendaciones relacionadas con riesgo reducible y corresponden al 10 % del total de las recomendaciones y su implementación requiere un análisis económico para minimizar los costos considerables de inversión en seguridad para la planta procesadora.
Se formularon 37 recomendaciones que corresponden a riesgo bajo, es decir aceptable en la que no se requieren implementar medidas de control de riesgo adicionales. Esto corresponde al 90 % de las del total de las recomendaciones.
La falta de información observada en los diagramas de procesos, impactaron en la aplicación de la metodología, ya que no se dispone de diagramas actualizados ni con información completa que ayuden a la identificación de otros nodos que pudieran ser de importancia, sin embargo, permitieron abordar la técnica de Hazop.
Financiamiento: esta investigación no recibió ninguna subvención específica de organismos de financiación de los sectores público, comercial o sin fines de lucro.
Agradecimientos: los autores agradecen a los ingenieros de riesgo de PDVSA, ingenieros de procesos de la planta procesadora de sábila que aportaron con su conocimiento para la versión final del manuscrito, así como a todo el personal que directa o indirectamente aportó al desarrollo de esta investigación.
Conflictos de interés: los autores declaran no tener ningún conflicto de intereses.
Referencias
1. Gallegos W. Revisión histórica de la salud ocupacional y la seguridad industrial. Revista Cubana de Salud y Trabajo. 2024;13(3):45-52. Disponible en: https://revsaludtrabajo.sld.cu/index.php/revsyt/article/view/600/612
2. Viña-Rodríguez J, Camejo Giniebra JJ, Castañeda Valdés A. Métodos de estudio más utilizados para el análisis de riesgos de procesos con sustancias peligrosas. Revista CENIC Ciencias Químicas. 2021;52(2):138-160. Disponible en: http://scielo.sld.cu/scielo.php?script=sci_arttext&pid=S2221-24422021000200138&lng=es&tlng=es
3. Aguilar K, Sosa S, Cadenas M. Uso de la Metodología HAZOP para el Análisis de Riesgo en Estaciones de Almacenamiento de Combustibles de Aviación. Artículos del Congreso Internacional de Investigación Academia Journals Celaya, México. 2021. Disponible en: https://ciateq.repositorioinstitucional.mx/jspui/bitstream/1020/542/1/Uso%20de%20la%20metodologia%20HAZOP.pdf
4. Storch de Gracia JM. Manual de Seguridad Industrial en Plantas Químicas y Petroquímicas. Fundamentos, Evaluación de riesgos y diseño. Volumen I. Madrid: Mc Graw Hill; 1998.
5. Barros Enriquez JD, Avemañay Morocho AM, Villafuerte Lopez MI, Punina Guerrero DJ, Valencia Rodriguez EG. Análisis e identificación de riesgos de operabilidad en procesos críticos de servicios petroleros, mediante la aplicación de la metodología HAZOP, en la industria ecuatoriana. LATAM Revista Latinoamericana de Ciencias Sociales y Humanidades. 2023;4(2):3804–3813. https://doi.org/10.56712/latam.v4i2.871
6. Buitrago B, Rodríguez L, Herrera E. Diseño del programa de gestión de seguridad de procesos bajo la norma OSHA 29 CFR 1910.119 para químicos altamente peligrosos en la industria de alimentos. Trabajo de grado de especialización. Universidad Ecci. Colombia. 2021. Disponible en: https://repositorio.ecci.edu.co/bitstream/handle/001/962/Dise%c3%b1o%20del%20programa%20de%20gesti%c3%b3n%20de%20seguridad%20de%20procesos%20bajo%20la%20norma%20osha%2029%20cfr%201910.119%20para%20qu%c3%admicos%20altamente%20peligrosos%20en%20la%20industria%20de%20alimento.pdf?sequence=1&isAllowed=y
7. Arriagada B. Adaptación de Metodología Hazop en el Estudio Funcional de Sistemas Automáticos, Aplicado a una Empresa de Producción de Alimento para Ganado. Memoria de titulación. Universidad Técnica Federico Santa María. Valparaíso, Chile. 2020. Disponible en: https://repositorio.usm.cl/server/api/core/bitstreams/a28b31cb-00a5-475d-a12c-b1993bd84853/content.
8. Arias M. Análisis de Riesgos en los Procesos de Producción del Acetileno y Propuesta de Elaboración de un Manual de Procedimientos. Tesis de Maestría. Universidad de Guayaquil. Guayaquil, Ecuador. 2014. Disponible en: https://repositorio.ug.edu.ec/server/api/core/bitstreams/e7c5ea8b-22e1-4b51-8594-a6067ddc2881/content
9. Arreola S. Diagnóstico y Evaluación Ocupacional de un Laboratorio Farmacéutico: Caso de Estudio. Tesis de Maestría. Instituto Politécnico Nacional. México, D.F. 2011. Disponible en: https://repositoriodigital.ipn.mx/bitstream/123456789/15822/1/TESIS%201.pdf
10. Peñaherrera V. Análisis Hazop de la unidad regeneradora de aminas. Tesis de Maestría. Universidad San Francisco de Quito, Ecuador. 2012. Disponible en: https://repositorio.usfq.edu.ec/handle/23000/1385
11. Castillo M. Evaluación de los riesgos operacionales mediante la metodología HAZOP en la empacadora Coral del Pacífico en la ciudad de Esmeraldas. Tesis de Maestría. Esmeraldas, Ecuador. 2021. Disponible en: https://repositorio.puce.edu.ec/server/api/core/bitstreams/65a898aa-1cf9-4fa9-9001-30ad2b82dd9d/content.
12. Petróleos de Venezuela S.A. Norma SI-S-19. Gestión y control de desviaciones. Manual de Seguridad Industrial. Volumen 1. Publicación de PDVSA. Venezuela. 2013.
13. Rodríguez Camacho ML, Navarrete Procopio M, Zezatti Flores V, Ochoa Ortíz A. Desarrollo de un entorno virtual para operar de forma segura el proceso de desorción utilizando el método HAZOP. Programación matemática Y Software. 2024;16(1):1–10. https://doi.org/10.30973/progmat/2024.16.1/1
14. Chirino CN. Algunos aspectos del manejo del paciente quemado en un servicio de cirugía infantil. A propósito de 47 pacientes pediátricos. IIa. Parte. Revista Argentina de Dermatología. 2023;104. Disponible en: http://www.scielo.org.ar/img/revistas/rad/v89n3/html/v89n3a05.htm
15. Pinheiro DF, Martins H dos S. Aplicación de la técnica HazOp como herramienta de gestión de riesgos en una distribuidora de bebidas. Investigación, Sociedad y Desarrollo. 2020;9(11):e3349119951. https://doi.org/10.33448/rsd-v9i11.9951
16. Almeida C. «Diseño de un procedimiento de actuación en caso de fuga de amoníaco en una planta cervecera industrial». Trabajo de fin de carrera. Universidad Internacional SEK. Quito, Ecuador. 2021. Disponible en: https://repositorio.uisek.edu.ec/bitstream/123456789/4117/1/Almeida%20Valencia%20Carlos%20Enrique.pdf.
| Received: 14 May 2024 | Accepted: 06 June 2024 | Published: 15 June 2024 |
Citation: Acacio-Chirino N, Cancino-Camperos J. Análisis de riesgos operacionales en una planta procesadora de sábila. Bionatura. 2024;9(2). DOI: http://dx.doi.org/10.21931/RB/2024.09.02.5
Peer review information: Bionatura thanks the anonymous reviewers for their contribution to the peer review of this work using https://reviewerlocator.webofscience.com/.
All articles published by Bionatura Journal are freely and permanently accessible online immediately after publication, without subscription charges or registration barriers.
Publisher’s Note: Bionatura stays neutral concerning jurisdictional claims in published maps and institutional affiliations.
Copyright: © 2024 by the authors. Submitted for possible open access publication under the terms and conditions of the Creative Commons Attribution (CC BY) license (https://creativecommons.org/licenses/by/4.0/).