Vol 7 No 4 2022- 63
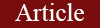
The Effect of Chicken Gallus gallus (Domestics) feathers on the sorption properties of polyurethane foam
1 University of Basrah, Polymer Research Center, Department of Materials Science, Iraq,
2 University of Basrah, College of Education/Qurna, Department of Biology, Iraq,
3 University of Baseah, College of Education/Qurna, Department of Biology , Iraq,
* corresponding authors: hamed.hamdi@uobasrah.edu.iq,
Available from: http://dx.doi.org/10.21931/RB/2022.07.04.63
ABSTRACT
A comparative absorption capability analysis was conducted using adapted polyurethane foam as crude oil Sorbents. The used Crude oil has been brought from the west of the Qurna city oil field with A.P.I. equals 22.2- 27. API measures how heavy or light a petroleum liquid is compared to water; crude oil’s sorption and absorption ratio amounts are investigated. The findings demonstrate that the absorption ratio of fluff feather to wing feather is very distinct. The fluff feather absorbed much more crude oil than the wings.
Moreover, much crude oil absorption causes the three types of feathers to plunge into crude oil. Owing to the disparity of the capillary structures of pure and modified polyurethane and the particular arrangement of the feathers, the absorption of modified polyurethane foam is beyond pure foam. The absorption ratio is saturated at (240-270) % (where the modified foam releases some additional volume of crude oil rather than the saturation ratio). Because of the cross-link density inside the modified foam, the last results were clarified. Also, we analyzed the effect of 10 holes on the absorption ratio in which the absorption is less than the unpinned ratio.
Keywords: Chicken feather, Qurna, West Qurna oil field, Iraqi crude oil, polyurethane, capillary structure.
INTRODUCTION
If oil leaks happen, we must then scrub the leaked oil to prevent humans and significant environmental problems. Human health and environmental protection are at threat 1. The ecological threats of spilled crude oil are not only related to water and sea life but also to the future of human beings. It is of great concern to use sorbents to minimize the chances of oil contamination and to consider the use of sorbents as one of the most economical and effective ways of cleaning up hydrocarbon pollution on the shoreline 2,3. Nature is the main source of many sorbents, and the industry created many modern sorbents 4-6. The mechanism of both natural and synthetic sorbents depends on inverting absorbed oil from the liquid phase to semi soil phase. In such a way, preventing spilled oil from controlling more water surfaces is easier and faster 7-10. The ultra-light polyurethane foams are one of significant oil absorbers. They can trap oil from oil-water mixtures several times its weight since that absorption capacity is associated with different ratios of bubbles spread within the foam matrix where more bubbles mean more oil absorption ability11-13. In natural conditions, the cross-linking density of polyurethane foam is considered to be one of the major factors that affect the absorption ability to both water or crude oil where the amount of taking water or oil by foams is highly related to that density since it affects the movement of molecules or jamming the way of absorbed molecules through the inside of polymer matrix14. In such a way, Polymer with such properties has taken much attention due to their wide area, different size formation, ease of handling, and transfer from one place to another. It is well known that sorbents can be either natural organic (eat moss, feathers), natural inorganic [clay, sand]», or synthetic [polyethylene, nylon15-17. Owing to their low density, low water absorption, and excellent physical and chemical resistance, synthetic polymers such as polypropylene are said to be suitable materials for marine oil-spill recovery 18-20. The main objective of this research is to compare the oil spill removal capacity of the small, medium, and large feathers and then to use the three different sizes of feathers to modify the foam. We based on the combination of natural and synthetic sorbents feather to adjust synthetic sorbents polyurethane foam and analyze the modified foam as spill oil sorbent in this paper.
MATERIALS AND METHODS
In this study, the used feather is obtained from the chicken (Gallus gallus domestics) bird. The used feathers were retrieved from the chicken farm site and washed multiple times to remove dust or filth. Two kinds of feather fluff and wings feathers were used. Each type of feather was distributed into the reaction container and mixed with reaction chemicals, as shown in figure (1). Di-isocyanates (part B) and polyols (part A) are reacted to produce polyurethane foam. A 1:1 (50:50) mixture ratio was used, which indicates that part A was equivalent to part B. The synthesis of Gallus gallus domestics-filled polyurethane foam was accomplished by combining 200 grams of part A and (200 g) of part B in a container, then adding (15 g) of Gallus Gallus domestics feathers directly to the mixing container.
The manual mixing of the used feathers and the reacting chemicals takes (3-4) minutes. At the end of the mixing phase, the mixture would rise, forming the upper layer, before being broken into random shape parts and left for one day. The crude oil brought from the Qurna West oil field has an A.P.I. of 22.2-27. For the absorption tests21, crude oil was poured into a (3 liters) exposed glass container with a diameter of 14.8 cm. In each experiment, a container was filled with (2 liters) of water and 300ml of oil. The amount of fat in the beaker was selected so there would be plenty of oil left during the absorption test. The dry weights of pure polyurethane foam parts are measured. Each piece was carefully mounted on the oil surface. After a specific time (As seen in the diagrams below), the samples were regularly taken out of the test jar. The wet surfaces of immersed foam are dried between tissue papers and measured directly to the nearest (+0.2 g). The samples are immediately returned to the specimen jar, and the tests are carried out. The steps of the method were repeated under the same conditions, but this time with modified polyurethane. On a weight basis, the sorbent’s oil sorption was measured. Oil absorption capacity is calculated by the formula [g/g] = [St–S0] /S0 that according to 22.
Where S0 denotes the original dry weight of a sorbent and St indicates the importance of the sample after immersion. Figure 1 shows the modified polyurethane foam added with feathers.

Figure 1. Shows the modified polyurethane foam added with feathers.
RESULTS
To use the modified polyurethane foam as a crude oil absorbent, we measured the absorption capacity of the feathers of chicken (Gallus domestics). Three different sizes of feathers were used (big, medium, and small). Figures 2, 3, and 4 show the changes made to the absorption ratio related to immersion time in crude oil. Figure (5) depicts the difference in the absorption ratio of modified polyurethane due to natural oil immersion time. The effect of pinholes and the obtained result in such a case are shown in figure (6). Figure (7) shows the shape of the modified foam after the immersion in crude oil and how the absorption of that oil blacked the inside matrix of that foam.

Figure 2. Absorption ratio of the medium feather as a function of immersion time.

Figure 3: Absorption ratio of the big-size feather as a function of immersion time in crude oil.

Figure 4. Absorption ratio of small feather as a function of immersion time.

Figure 5. Absorption ratio of modified polyurethane foam as a function of immersion time.

Figure 6. The effect of pinholes on absorption ratio of modified polyurethane.

Figure 7. The shape of modified polyurethane foam after immersion in crude oil.
DISCUSSION
It is evident from the last figures (2, 3, and 4) that the immersion time is limited to one minute. After that, all three feather sizes diving into the crude oil, indicating the heavy amount of crude oil absorbed by the feather. A second noticeable thing from the last figure is that the absorption capacity is more prominent with a small feather than that with a medium and large size feather. The previous result is due to the unique structure of feather-like barbs linking density per feather 23,24. Figure 5 indicates that the time range starts with one minute to 240 minutes. The saturation absorption ratio is restricted to 240 %, which is more than pure polyurethane foam. We must note that we used big feathers since they had the highest absorption ratio, as shown in the last three photographs—[105 %].
Moreover, in another sample of modified foam, the reached saturation ratio is 270%. The difference between these two ratios is surely related to the geometrical distribution of feathers into the foam matrix. This saturation and limitation of the absorption capacity are also due to the heavy cross-linking density of polyurethane foam chains. This cross-linking density prevents further oil molecules from taking into the foam since no more space between chains is available in that foam. Thus we see the absorption ratio is increasing with time, especially at 120 minutes, but it decreases at 240 minutes. The last decrease in absorption ratio may explain in terms of no space to control molecules of oil into it due to the high cross-linking density. Thus for the previous result, we moved to study the effect of pinholes on the absorption ratio. The reason for choosing pinholes is to make a new way for oil molecules to cross their way up into the polyurethane foam matrix. We decided 10 holes per (25cm2) distributed through the foam matrix. The diameter of each pinhole was (1mm). Figure 6 shows less absorption ratio is obtained, but no absorption saturation is reached. Even though they managed new ways into the matrix of foam, the lower absorption ratio still has much space in that foam.
More tests are needed to determine the appropriate ratio between the two components, A and B, of polyurethane. Compared with other natural additives added to polyurethane foam, the absorption ratio obtained in this study is less than that obtained by other researchers 25-28. Aside from the lower absorption potential, natural organic sorbents include hay, feather, straw, peat moss, and other carbon-based materials29-32. Natural crude oil sorbents have the unfavorable characteristics of being gritty, difficult to use under windy weather and having no oil absorbency. Furthermore, specific natural organic sorbents accumulate oil and water, allowing the sorbents to sink. In such a manner, the modified foam seems to solve the problematic use under windy conditions, but the small absorption capacity is still less than the aim of this study 33. It is vital to note that the immersion time ranges from one minute to three minutes, with a two-minute break in between.
CONCLUSIONS
The absorption action is related to the kind and size of the used feathers. The fluff feathers are becoming more suited for the absorption of crude oil and the modification of polyurethane foam as an absorbent. The absorption capacity is larger with a small feather than with a medium and large size feather. Furthermore, the absorption ratio of modified polyurethane is improved due to capillary structure improvements made to the polyurethane foam, which is attributed to adding a chicken feather. Modified polyurethane has significant potential as an oil sorbent, especially within the first hour of an oil leak or spill. The 120-minute duration is long enough to achieve a saturation absorption ratio. Pinholes have the opposite effect on the absorption properties of modified polyurethane foam.
Acknowledgment: Thanks going for all who support us.
Conflict between authors: No conflict
Funds: self by authors
REFERENCES
1. Laffon B, Pásaro E, Valdiglesias V. Effects of exposure to oil spills on human health: Updated review. Journal of Toxicology and Environmental Health, Part B. 2016 May 18;19(3-4):105-28.
2. Abu Bakar Salleh», Farinazleen Mohamad Ghazali, Raja Noor Zaliha Abd Rahman and Mahiran Basri. Bioremediation of Petroleum Hydrocarbon Pollution. Indian Journal of Biotechnology, Vol 2, July 2003, pp 411-425.
3. Pandey S. and Alam A., Peat moss: A hyper-sorbent for oil spill cleanup-a review. Plant Science Today., 2019, 1;6(4):416-9.
4. Semenkova A, Belousov P, Rzhevskaia A, Izosimova Y, Maslakov K, Tolpeshta I, Romanchuk A, Krupskaya V. U (VI) sorption onto natural sorbents. Journal of Radioanalytical and Nuclear Chemistry. 2020 Oct;326(1):293-301.
5. Labus K. Comparison of the Properties of Natural Sorbents for the Calcium Looping Process. Materials., 2021, 24;14(3):548.
6. Yurak V, Apakashev R, Dushin A, Usmanov A, Lebzin M, Malyshev A. Testing of natural sorbents for the assessment of heavy metal ions’ adsorption. Applied Sciences. 2021 Apr 20;11(8):3723.
7. Blachnio M, Derylo-Marczewska A, Charmas B, Zienkiewicz-Strzalka M, Bogatyrov V, Galaburda M. Activated carbon from agricultural wastes for adsorption of organic pollutants. Molecules. 2020 Nov 3;25(21):5105.
8. Jóźwiak T, Filipkowska U, Rodziewicz J, Mielcarek A, Owczarkowska D. Zastosowanie kompostu jako taniego sorbentu do usuwania barwników z roztworów wodnych. Rocznik Ochrona Środowiska. 2013;15.
9. Atta AM, Arndt KF. Swelling and network parameters of high oil‐absorptive network based on 1‐octene and isodecyl acrylate copolymers. Journal of applied polymer science. 2005 Jul 5;97(1):80-91.
10. Brakstad OG, Lewis A, Beegle-Krause CJ. A critical review of marine snow in the context of oil spills and oil spill dispersant treatment with focus on the Deepwater Horizon oil spill. Marine pollution bulletin. 2018 Oct 1;135:346-56.
11. Starov V, Trybala A, Johnson P, Vaccaro M. Foam Quality of Foams Formed on Capillaries and Porous Media Systems. Colloids and Interfaces. 2021 Feb 8;5(1):10.
12. Kouko J, Prakash B, Luukkainen VM, Jäsberg A, Koponen AI. Generation of aqueous foams and fiber foams in a stirred tank. Chemical Engineering Research and Design. 2021 Mar 1;167:15-24.
13. Barode J, Aravind U, Bhogi S, Muduli B, Mukherjee M. Mg and mg-based blowing agents for aluminum foam. Metallurgical and Materials Transactions B. 2021 Feb;52(1):292-304.
14. Keshawy M, Farag RK, Gaffer A. Egyptian crude oil sorbent based on coated polyurethane foam waste. Egyptian Journal of Petroleum. 2020 Mar 1;29(1):67-73.
15. Asadpour R, Sapari NB, Tuan ZZ, Jusoh H, Riahi A, Uka OK. Application of Sorbent materials in Oil Spill management: A review. Caspian Journal of Applied Sciences Research. 2013 Feb 1;2(2): 46-58.
16. Włodzimierz Kończewicz, Sylwia Polasz and Kinga Rogowska, USING SORBENTS FOR OIL SPILL CLEAN-UP IN PORTS AND COASTAL AREAS, Journal of KONES Powertrain and Transport, Vol. 26, No. 4 2019 , pp:113-117.
17. Balintova M, Demcak S, Pagacova B. A study of sorption heavy metals by natural organic sorbents. environments. 2016;2(11):189-94.
18. Politayeva NA, Smyatskaya YA, Dolbnya IV, Kasobov LS, Rakhimov DB, Zaripova DA. Research of pH influence on sorption properties of sorbents on a basis of residual biomass of microalgae Chlorella sorokiniana and duckweed Lemna minor. InE3S Web of Conferences 2019 (Vol. 124, p. 01050). EDP Sciences.
19. Asemave K, Thaddeus L, Tarhemba PT. Lignocellulosic-based sorbents: a review. Sustainable Chemistry. 2021 Apr 10;2(2):271-85.
20. Salisu ZM, Ishiaku SU, Abdullahi D, Yakubu MK, Diya’uddeen BH. Development of kenaf shive bio–mop via surface deposit technique for water remediation from crude oil spill contamination. Results in Engineering. 2019 Sep 1;3:100020.
21. Hamed A. hamdi, Murtadhafaraj, NadhimA.Abdullah, The Effect of Gray Heron on oil Sorption Capacity of Polyurethane Foam, J. Missan Researches, 12(24), 2016, pp:271-279.
22. Li H, Liu L, Yang F. Oleophilic polyurethane foams for oil spill cleanup. Procedia Environmental Sciences. 2013 Jan 1;18:528-33.
23. Heers AM, Tobalske BW, Dial KP. Ontogeny of lift and drag production in ground birds. Journal of Experimental Biology. 2011 Mar 1;214(5):717-25.
24. Pap PL, Vincze O, Wekerle B, Daubner T, Vágási CI, Nudds RL, Dyke GJ, Osváth G. A phylogenetic comparative analysis reveals correlations between body feather structure and habitat. Functional ecology. 2017 Jun;31(6):1241-51.
25. Hoang AT, Le VV, Al-Tawaha AR, Nguyen DN, Al-Tawaha AR, Noor MM, Pham VV. An absorption capacity investigation of new absorbent based on polyurethane foams and rice straw for oil spill cleanup. Petroleum Science and Technology. 2018 Mar 4;36(5):361-70.
26. Aisien FA, Hymore FK, Ebewele RO. Comparative absorption of crude oil from fresh and marine water using recycled rubber. Journal of Environmental Engineering. 2006 Sep;132(9):1078-81.
27. Sayyad Amin J, Vared Abkenar M, Zendehboudi S. Natural sorbent for oil spill cleanup from water surface: environmental implication. Industrial & engineering chemistry research. 2015 Nov 4;54(43):10615-21.
28. Vlaev L, Petkov P, Dimitrov A, Genieva S. Cleanup of water polluted with crude oil or diesel fuel using rice husks ash. Journal of the Taiwan Institute of Chemical Engineers. 2011 Nov 1;42(6):957-64.
29. Carmody O, Frost R, Xi Y, Kokot S. Adsorption of hydrocarbons on organo-clays—implications for oil spill remediation. Journal of Colloid and Interface Science. 2007 Jan 1;305(1):17-24.
30. Bastani D, Safekordi AA, Alihosseini A, Taghikhani V. Study of oil sorption by expanded perlite at 298.15 K. Separation and Purification Technology. 2006 Dec 1;52(2):295-300.
31. Annunciado TR, Sydenstricker TH, Amico SC. Experimental investigation of various vegetable fibers as sorbent materials for oil spills. Marine pollution bulletin. 2005 Nov 1;50(11):1340-6.
32. Suni S, Kosunen AL, Hautala M, Pasila A, Romantschuk M. Use of a by-product of peat excavation, cotton grass fibre, as a sorbent for oil-spills. Marine pollution bulletin. 2004 Dec 1;49(11-12):916-21.
33. Ding L, Li Y, Jia D, Deng J, Yang W. β-Cyclodextrin-based oil-absorbents: Preparation, high oil absorbency and reusability. Carbohydrate Polymers. 2011 Feb 1;83(4):1990-6.
Received: September 22, 2022 / Accepted: October 18, 2022 / Published:15 November 2022
Citation: Abdullah N A, Hamdi H A, Shaban A D. The Effect of Chicken Gallus gallus (Domestics) feathers on the sorption properties of polyurethane foam. Revis Bionatura 2022;7(4) 63. http://dx.doi.org/10.21931/RB/2022.07.04.63